Selective growth of ZnO micro- and nano-structures on fs-laser processed metallic Zn substrates for large area applications
- A novel two-step process using femtosecond lasers and low-temperature heat treatment enables large-scale production of micro- and nanostructured ZnO surfaces.
- The resulting ZnO structures have high photocatalytic activity, effectively degrading contaminants such as rhodamine B, and open up possibilities for the creation of reusable catalysts.
Madrid / January 23, 2025
A scientific team led by the Laser Processing Group of the Institute of Optics has published in the Journal of Alloys and Compounds a new method to produce micro and nanostructured ZnO surfaces, capable of degrading 43% of the contaminant rhodamine B in water in 90 minutes.
Latest news
Natural Slab Photonic Crystals as Biogenic, Customizable Nanomaterial for Label-Free Detection
Scientists demonstrate the potential of diatoms as photonic nanomaterials for sensing. The biogenic material is extracted directly from the microalgae and does not require markers, simplifying and reducing the cost of the sensor manufacturing process. Madrid / April...
The team, made up of researchers from the Institute of Optics (IO-CSIC), the Complutense University of Madrid, the Carlos III University of Madrid and the KU Leuven university, has developed a new two-step method to produce such ZnO surfaces. The process involves irradiation of zinc metal foils with high repetition rate femosecond laser pulses followed by low temperature (380°C) heat treatment in argon atmosphere. This method results in LIPSS (Laser Induced Periodic Structures) structures coated with ZnO nanowires and columns covered by a relatively thick ZnO layer, which substantially increases the surface area of the material in contact with the contaminant and thus its effectiveness.
The mechanism of ZnO growth during heat treatment is determined by the preconditions of laser processing. The team has studied the different growth mechanisms with the different thicknesses of ZnO induced by the first phase of laser irradiation: nanowire growth by a vapor-liquid-solid mechanism for very thin initial oxide layers, formation of ZnO agglomerates by a vapor-solid mechanism for intermediate oxide thicknesses and complete inhibition of the growth of ZnO nanostructures if the initial oxide layer induced by laser processing is too thick.
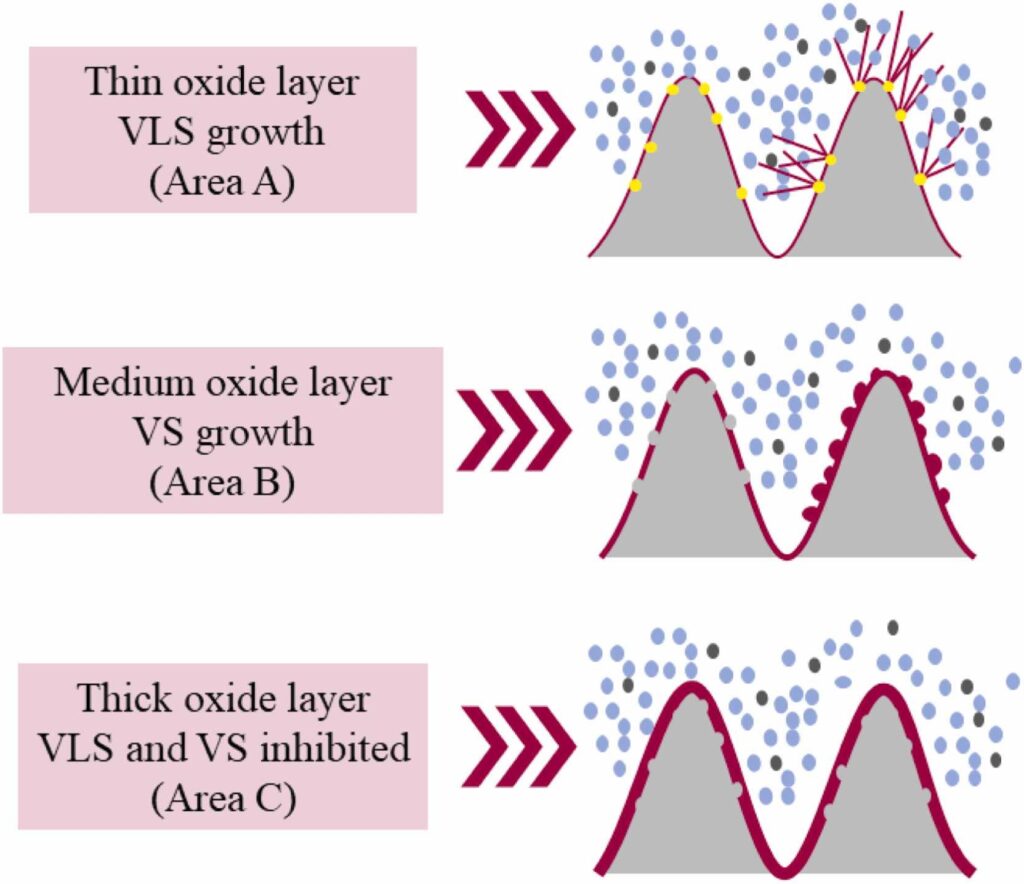
In photocatalysis, one of its most important applications, ZnO is used to degrade persistent organic pollutants (POPs) in water. These pollutants are resistant to environmental degradation and cannot be completely removed through current water treatment processes.
To remove these contaminants, the ZnO structure absorbs photons that are used by electrons to gain high energies, allowing them to oxidize organic contaminant molecules into carbon dioxide, water, and other inorganic byproducts.
The two-step process for producing ZnO surfaces
To produce micro- and nanostructured ZnO surfaces, the researchers used a two-step process. First, they irradiated metallic zinc sheets with femtosecond laser pulses at high repetition rates (100-500 kHz) and fast scanning speeds (cm/s) in air at atmospheric pressure. This laser structuring process has two main purposes: to modify the surface morphology to increase its specific surface area and to oxidize the surface to facilitate the subsequent growth of ZnO micro- and nanostructures during heat treatment. After laser irradiation, the sheets were heat treated in an argon flow at 380°C for 5 hours. This thermal treatment was performed to promote spatially selective growth of ZnO micro- and nanostructures. After the growth of the ZnO, the team analyzed the shape, composition, crystal structure, and luminescent properties of the material at different stages of the process. This analysis allowed them to determine the role of the different processing parameters (laser irradiation and thermal treatment) on the properties of the resulting ZnO.
Article: R. Ariza, A. Urbieta, A. Ferreiro, M.E. Rabanal, P. Fernández, J. Solis. “Selective growth of ZnO micro- and nano-structures on fs-laser processed metallic Zn substrates for large area applications”. Journal of Alloys and Compounds. Volume 1010, 5 January 2025, 177797
IO-CSIC Communication
cultura.io@io.cfmac.csic.es
Related news
The Institute of Optics joins the celebration of 11F
Full and equal access and participation of women and girls in science and technology Madrid / January 31, 2025In recent decades, the international...
Optoplasmonic tuneable response by femtosecond laser irradiation of glass with deep-implanted gold nanoparticles
Ion implantation of Au2+ at MeV energies has enabled the creation of nanoparticles embedded at greater depth, resulting in a Fabry-Perot cavity...
On November 20th, David Grojo from CNRS will give a lecture entitled “New Dimensions Open to Ultrafast Laser Material Modifications”
Madrid / November 13, 2024On Wednesday, November 20th at 11:30 a.m. we will have a seminar organized by the Laser Processing Group in the conference...